How bonded anchors work – a practical guide
Today’s construction technologies offer a wide range of solutions to meet the requirements of even the most challenging projects. That is why, before choosing a chemical fixing, you should first realise how bonded anchors actually work? Let’s take a closer look at this matter.
The key to understanding the potential of bonded anchors is their unique capacity to form extremely strong bonds. The variety of the available resins allows you to choose an anchor against the specific requirements of each substrate and application. Most of them perform well in concrete, in the zones of both compression and tension, yielding exceptional strength and reliability, while the polyester anchor, which is also fit for slightly weaker materials, is considered suitable for both advanced construction projects as well as home repairs and renovations.
What are bonded anchors?
In construction engineering, anchors perform a very important function, ensuring the stability and safety of structures. The high loads they are capable of carrying make chemical fixings an increasingly popular solution among contractors. Conventional mechanical anchors, such as those dedicated to concrete, form joints with the base material by way of expansion forces, generating high stresses in the substrate, while all bonded anchors owe their properties to the adhesion phenomenon.
In practice, the choice between chemical and mechanical anchors depends on the specific project and installation conditions. Properties such as the load capacity of bonded anchors as well as their capability of absorbing and distributing forces in the material make them a standard in the contemporary construction industry, where precision and adaptation to diverse technical conditions are paramount. Such solutions make it possible to successfully complete even complicated projects, ensuring durability and reliability for years.
Types of bonded anchors
The contemporary market abounds in different kinds of bonded anchors. They are mainly distinguished according to the base material for which a given anchor is suitable. And understanding this breakdown is crucial to the choice of the right bonded anchor.
Rawlplug’s bonded anchors intended for concrete clearly stand out as innovative and infallible, becoming construction professionals’ solution of choice. Before making a purchase, it is advisable to consider the specific requirements of a given project, including resistance to external factors or the type of loads expected to affect the anchor. All these aspects have a direct impact on the ultimate choice of the right kind of chemical fixing solution.
You can read more about the application and handling of bonded anchors under extreme weather conditions on our blog.
Bonded anchors. What can you find on the market?
- Styrene-free polyester anchors are particularly valued for the wide range of substrates in which they can be applied.
- Vinyl ester anchors, known for their exceptional strength and resistance to chemical compounds, are ideal for chemically aggressive environments. They are also available in capsules.
- Hybrid anchors, combining the best features of polyester and vinyl ester anchors, represent a versatile solution for the most demanding applications.
- Epoxy anchors, being the strongest chemical anchors among the available solutions, outdistance other fixings with their unparalleled performance and superior properties.
Understanding the differences between individual types of bonded anchors enables making informed choices of the solutions best suited for specific applications.
How does a bonded anchor work? Design of bonded anchors – epoxy anchor example
Thinking of bonded anchors, you rarely consider what underpins their extraordinary strength. How come these apparently uncomplicated substances can bond different materials so effectively, withstanding weight, pressure, and even extreme weather conditions? The secret lies in their ingredients – highly specialised mixtures of different compounds. Understanding the properties of an anchor can allow you to realise its potential under construction projects.
Did you know that…?
The chemical ingredients of bonded anchors in cartridges are contained separately. This is necessary, because if the resin and the hardening agent were kept together, they could react with each other while still inside the packaging. With the components separate, the mixture retains its properties until used at the application point. This solution guarantees the efficiency and reliability of bonded anchors on the construction site!
The cartridge-type bonded anchor represents a two-component system, meaning that it comprises two separate parts, each containing different ingredients that are mixed during application. Every now and again, you may find these fixings intuitively referred to as two-component anchors.
A two-component cartridge contains:
- Component A: typically a resin (e.g. epoxy), with loose inorganic fillers that can increase mechanical strength and rheological additives that control viscosity;
- Component B: hardening agent enabling the resin to bind, with fillers added to improve structural properties.
The resin mixture is a substance which, once cured, forms a strong and durable bond. There are several types of resin, and it is important to remember that each has its own unique characteristics and is dedicated to specific solutions. The resin components may contain:
1. Hardening agents which enable the bonding process – these substances react with resins, causing them to set.
The hardener type is matched to the resin type and the intended properties of the final product, and depending on the amount, it can slow down or speed up the setting process. There are two groups of hardeners:
- Amine hardeners, typically used in epoxy anchors.
- Peroxide-based hardeners for unsaturated resins, i.e. polyester and vinyl ester resins.
2. Fillers, added to improve the mechanical properties of the mixed compound and to control its viscosity. Various filler types can be used, including:
- sand,
- quartz, or
- calcium carbonate.
All these natural minerals are fillers capable of increasing the mechanical strength and reducing the shrinkage of resins as they are setting.
3. Special additives used to regulate the gel time, such as:
- inhibitors,
- wetting and dispersing additives,
- process additives,
- thickening additives, and
- dyes.
The properties of anchors, such as tensile strength, compressive strength, and capacity to withstand dynamic loads, are directly linked with the quality of the materials used and the right formulation. This makes epoxy anchors suitable for a wide range of fixing applications in concrete, masonry, or stone, offering safety and stability for years.
What are the advantages of bonded anchors?
The advantages of bonded anchors prove particularly important for projects which require fixings capable of coping with heavy loads. Thanks to their exceptional load capacity, elements fixed using a bonded anchor remain stable even under the heaviest loads. However, it is not only the load capacity of bonded anchors that counts among their unique properties.
- One of the main advantages of bonded anchors is their mechanical strength, i.e. the capacity to withstand certain mechanical loads without becoming damaged or deformed, or losing operating properties. Thanks to their mechanical strength, these anchors guarantee durability and reliability of joints, in which they clearly outperform traditional fixing methods.
- Bonded anchors effectively dissipate stresses in the base material, ensuring stability, even in heavy-duty applications, minimising the risk of substrate damage.
- The high strength of bonded anchors makes them suitable for installation jobs where prolonged resistance to dynamic and static loads is required. The service life of a bonded anchor used for fixing purposes, i.e. the time for which the anchor retains its mechanical and adhesive properties, can vary depending on a number of factors. As a rule of thumb, when properly applied under adequate conditions, bonded anchors can remain fully functional for as long as several decades, and the chemical anchors from Rawlplug – up to a hundred years!
Interesting fact!
Did you know that Rawlplug’s bonded anchors retain their full operating capacity for up to 100 years? Making the most of an innovative technology and subject to new procedures of verification under the European Assessment Document (EAD), Rawlplug’s resins have received formal confirmation of their exceptional durability and quality. Their 100-year service life makes them an excellent choice for projects that require long-lasting reliability.
- Bonded anchors are also known as being suitable for operation under a variety of weather and chemical conditions, which makes them highly adaptable. Additionally, being essentially fluid in substance, bonded anchors can be used in hard-to-reach places where traditional mechanical anchors cannot be installed.
- Precise dosing and accurate application of bonded anchors increase fixing efficiency. Chemical anchoring systems enable high-accuracy dosing and application of resin at the fixing point, which minimises waste and streamlines installation work.
- Chemical anchors can be applied in close proximity of substrate edges or other anchorage points, which proves particularly useful in places where it would be impossible or risky to use traditional mechanical anchoring methods on account of the base material cracking risk.
You can find more information about the minimum edge distance of the anchors applied in concrete in our dedicated post!
What are the disadvantages of bonded anchors?
Despite their undeniable advantages and the benefits they bring, bonded anchors have some disadvantages which should be taken into account. Prior to chemical fixing, you should consider the specific conditions in which the anchor will operate.
- How much time needs to elapse before a bonded anchor becomes operational? One of the limitations to the use of bonded anchors in construction work is their performance variability caused by temperature changes. Temperature-related restrictions can significantly affect resin curing, and by that means, also the process in which the anchor’s full strength is assumed to be attained. Low temperatures can slow down the chemical reaction, thus extending the setting time, while high temperatures can accelerate this process, but also weaken the resin structure, leading to reduced durability and strength.
- For these reasons, both the setting time and the curing time of bonded anchors can be counted among their disadvantages. Setting time is the time required for the chemical compound to begin to harden to the point where it no longer moves inside the anchorage hole. It determines how quickly the elements embedded using a bonded anchor will start to stabilise. Curing time, on the other hand, is the time it takes for the anchor to reach its full mechanical and adhesive strength.
- Price of a bonded anchor. Although bonded anchors may seem more expensive in purchase and installation compared to conventional mechanical fixings, their advanced properties and load capacities, second to no solutions available on the market, make them an investment that saves time and money in the long run. Owing to their performance, on-site working time can be significantly reduced, which is particularly important for large projects. Additionally, having chosen the CFS+ anchors, you can optimise expenditure and achieve even greater cost efficiency.
Must-know fact!
Using the cartridge-free system (CFS+), you can significantly reduce plastic consumption. At Rawlplug, in the production of our high-end CFS+ resin film packs, we currently use only a tenth of the plastic that was once needed to produce conventional cartridges. Minimising plastic consumption and reducing waste are key objectives in our company’s long-term sustainability strategy.
- How to apply bonded anchors? The application of a bonded anchor requires accuracy and attentiveness, and that includes adequate drilling of holes, cleaning them from dust and other impurities, as well as highly precise mixing of ingredients and application of the compound. Any mistakes made in the course of these processes can significantly affect the performance, and thereby also the load capacity, of bonded anchors.
- Different types of anchors also mean different application procedures. All bonded anchors can be used in concrete, but when installing in a different base material, you need to reach for one particular anchor type, i.e. polyester resin, paired with a mesh sleeve needed to conduct correct bonded anchor application in a hollow substrate. Some anchors, unlike other resins, are characterised by limited chemical resistance, which also needs to be taken into account, depending on the environmental conditions of the installation job.
Intended use of bonded anchors
Bonded anchors come in handy in many situations, especially where traditional fixing methods prove insufficient. They are perfectly suited for jobs where strong and durable fixing of structural components to materials such as concrete is required, but they are also ideal for fixing near concrete slab edges, where other methods could cause cracks or weaken the substrate structure.
Additionally, chemical anchoring systems are particularly suitable for heavy loads. The exceptional load capacity of bonded anchors means that they are capable of carrying loads that no conventional mechanical anchors could withstand. This makes them an excellent choice for structures exposed to intense loading, such as bridges, industrial machinery, or facade elements.
Professional bonded anchors are also recommended for application where the accuracy and strength of anchorage is crucial, e.g. in restoration of historic buildings, where the preservation of the existing structure comes as a priority and the ability to accurately apply the anchor minimises the risk of the base material damage. Chemical anchors are also specifically intended for demanding environments, such as public buildings and hospitals, where safety is paramount.
Moreover, bonded anchors prove ideal for application in places exposed to harsh weather or chemicals, where resistance to corrosion and other harmful conditions is required.
You can read more about the differences between bonded and mechanical anchors in our blog post.
How to perform correct fixing using a bonded anchor?
Correct fixing of various materials using bonded anchors is fundamental to ensuring the stability and security of any structure. The choice of the right anchoring solution starts with an assessment of the base material, the fixing conditions, and the load capacity of a given chemical anchor. It is always good to be sure that the elements to be installed using a bonded anchor will remain firmly and securely fixed for a long time.
Step-by-step instruction of bonded anchor application
- The first step to take when performing installation by means of bonded anchors is obviously to drill a hole using a suitable drill bit.
- Remember to thoroughly clean the hole of any dust, dirt, and any debris, using a cleaning brush and a pump.
Rawlplug’s recommended product!
In order to speed up the hole cleaning before applying the bonded anchor, a good solution is to use the Dustlessdrill bit, which removes borings while the hole is being drilled.
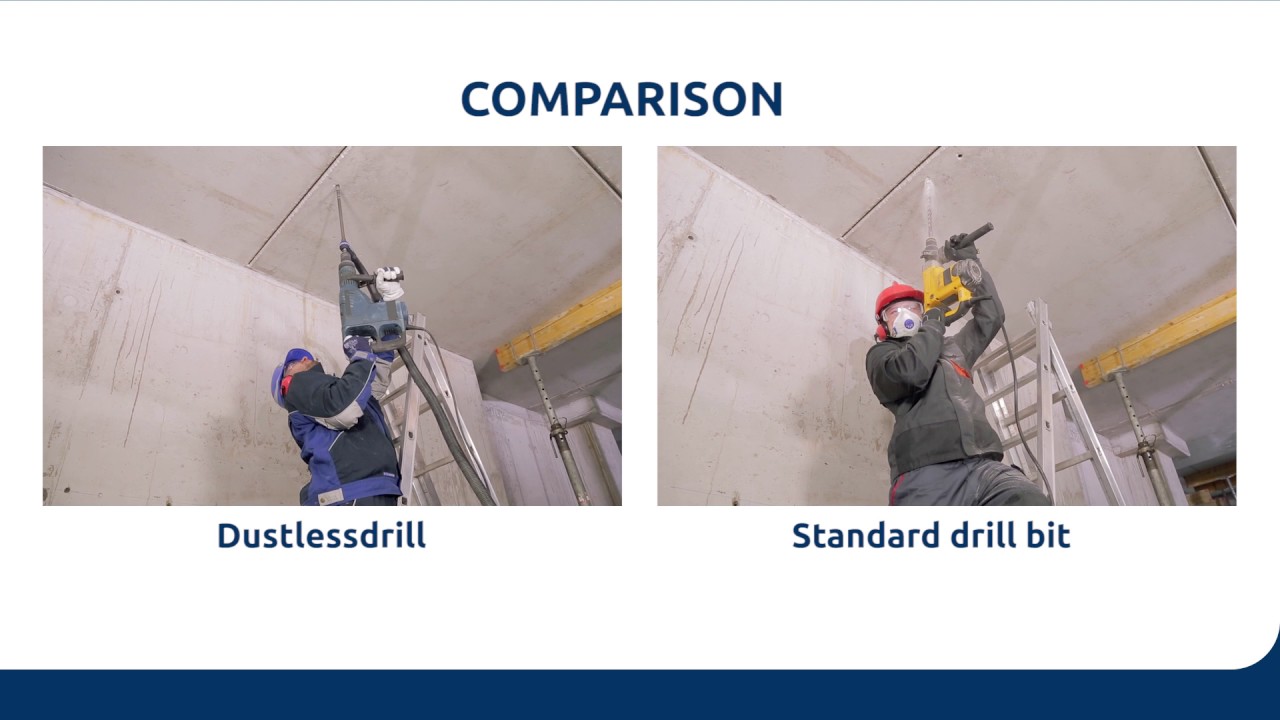
Have a look at Rawlplug’s Dustlessdrill bit in action and check how it can help you speed up work:
3. Next, with a cartridge system in use, make sure to thoroughly mix the two anchor components and fill the hole correctly with resin using a dedicated dispenser gun. When applying the resin in concrete, fill the hole to 75% of its depth, while in porous substrates, such as brick or hollow blocks, the recommendation is to insert a mesh sleeve and fill the hole in 100%. Adequate distribution of resin ensures even anchor adhesion to the substrate.
4. The element being embedded in the substrate should be placed inside the hole before the resin has fully set, since the chemical bond must form a lasting and strong joint with the base material. The time it takes for the resin to begin to harden varies depending on the anchor type and the environmental conditions. In many cases, acting quickly and with utmost precision is a must.
Related articles
12 May 2025
#Bonded anchorR-KER II now ETA - approved for seismic category C2!
17 February 2025
#SiteTestingOn-site fixing test – R-KEXII chemical anchor with R-STUDS rod
17 February 2025
#ReferenceObjectsThe first metro line in Ho Chi Minh City with Rawlplug anchors!
23 December 2024
#SiteTestingSite test of fixings - R-KEM-II chemical anchor and R-STUDS rod